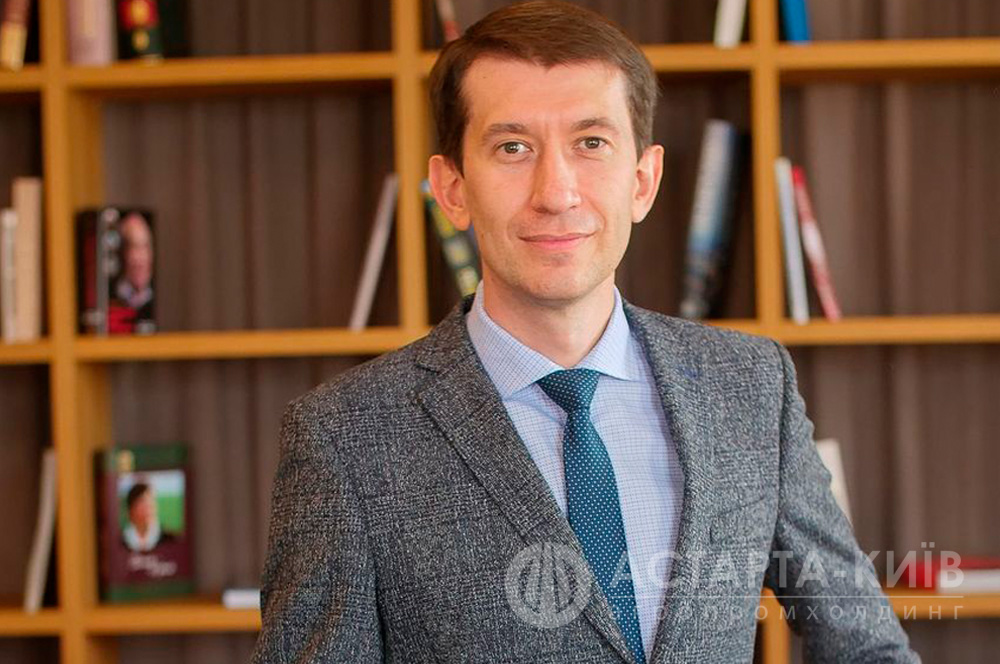
The Astarta’s Operational Performance Management Office summed up the results of its two-year programme under the Operational Improvement System Astarta (OISA).
The economic benefits are estimated at UAH28m. Almost 900 employees of the Company became its active participants, e.i. nearly 14% of total headcount. On average UAH32k of economic benefit was achieved per participant of OISA.
Over two years more than 2 100 ideas were submitted in all segments of the Company’s business. Thirty-one operational improvement projects had been implemented. Fourteen “kaizen projects” are currently in the process of realisation.
The Company paid UAH2.5m in bonuses to the authors and implementation teams.
— We are actively developing a culture of internal entrepreneurship in Astarta so every employee can offer any proposal or idea. For example, our staff has developed a prototype of a self-propelled video probe that travels through the pipe systems of the elevator and allows one to get online images of their technical condition on a mobile phone. Now the work, which used to take two months and required the dismantling of these pipes, takes only two days. The technology of wireless video transmission of such work, combined with the creative approach of people, gives a sizeable economic result, — says Eugene Kovnir, the Head of the Astarta Operational Performance Management Office.
For reference
The Operational Improvement System Astarta (OISA) is a management system designed for creation of perfect business processes and the involvement of each employee in the process of continuous improvement.
It is aimed at improving the efficiency of operations and management activities of the business, flexibility and speed.